The Ultimate Guide to Pick and Pack Fulfillment and Logistics
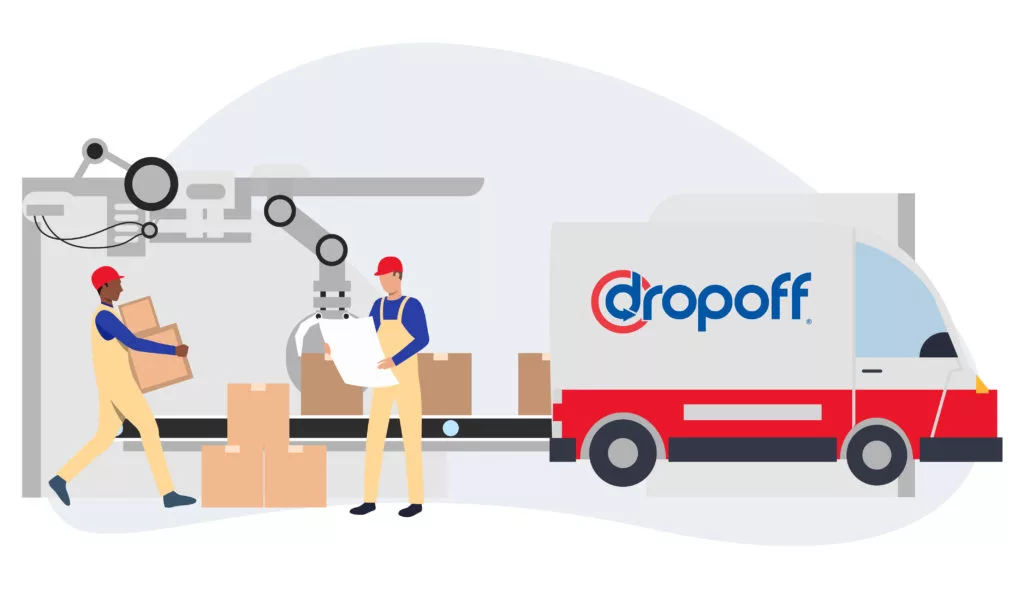
If you’re looking for a comprehensive guide to pick and pack fulfillment and logistics, you’ve come to the right place. In this blog post, we’ll discuss pick and pack, the benefits of using a pick and pack service, and how to choose the right fulfillment partner for your business.
So whether you’re just starting out and need some advice on getting started or looking for ways to improve your current pick and pack process, read on!
What Is Pick and Pack?
The term “pick and pack” refers to taking goods that customers have purchased and putting them into packages for shipping.
This includes removing the items from pick and pack warehouse or storage shelves, putting them into a package, and adding packing slips, invoices, flyers, advertising, and other packing materials the merchant needs.
This system eliminates the need for repacking, which makes packing faster. It is mainly used by online retailers for the delivery of small orders.
Moreover, pick and pack practices are relatively similar to on-demand logistics.
Top 7 Benefits of Using a Pick and Pack System: Why Online Businesses Love It
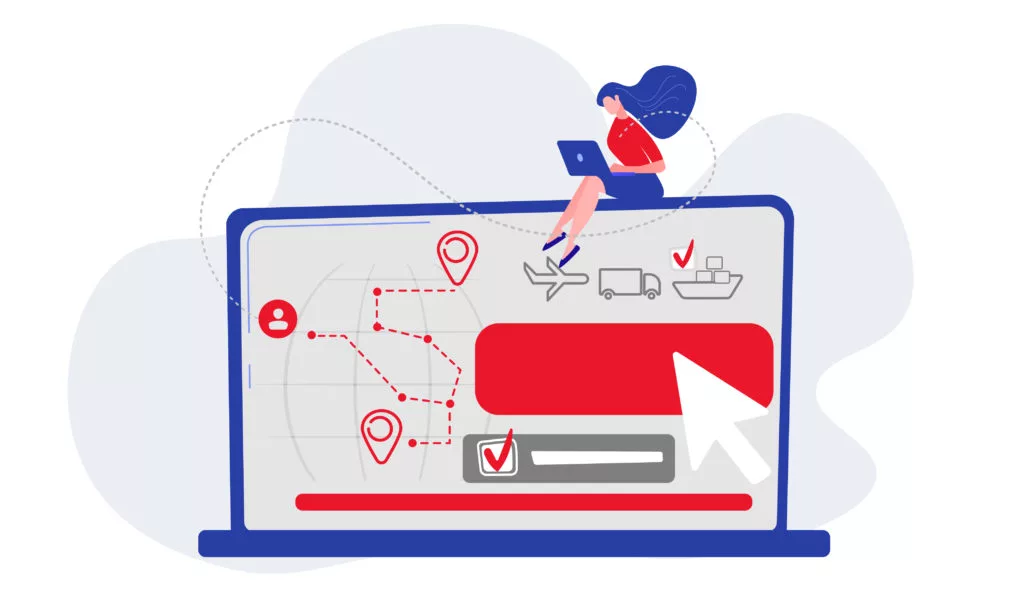
1. Increased Packing and Shipping Speed
The first benefit is that your items will be shipped faster. You can either hire employees who are good at packing quickly or train your current employees to do it quickly. However, hiring employees cost more money, and training employees cost more time. This is why business owners often resort to outsourcing to third-party logistics companies for pick and pack services as it is far less time-consuming and more cost-efficient.
2. Greater Efficiency
The right pick and pack approach can save time, which produces a higher efficiency. This approach increases the speed of order fulfillment activities, including the processing speed of employees when order picking. It also enables products to be inventoried, stored, picked, and packed in one location. This means that it is easier to put products together from different places and send them to other places for packing and labeling.
3. Better Organization
To have a successful pick and pack system, you need to have an organized warehouse. This means that all the items in the master cartons should be clearly labeled or put together in similar groups. A master carton is the large outer container that you see first when receiving a package. It’s often marked with the number of units inside and shipping directions.
Overall, having an organized warehouse will make the job of the workers effortless. There’s no need to waste time going from one carton to another looking for what you need. They also don’t have to stop to ask someone else where something is.
4. Better Accuracy
An organized pick and pack system improve your order accuracy. When fulfilling orders for your customers, sending them the right product is essential. This means that you need to be accurate in your packing.
5. Higher Productivity
It can be difficult to maintain a high level of productivity in the workplace at times. With a pick and pack system, the whole operation demands a high level of attention, requiring staff members to remain productive at all times. Additionally, the pick and pack system comes with several order picking methods that are proven to be effective in increasing overall employee productivity.
6. Less Expensive
Although pick and pack is a cheaper option, it is not free. There are charges that can come up during the order fulfillment process.
Common charges and fees for pick and pack services include:
- Order receiving
- Order processing
- Employee training
- Hiring new staff for pick and pack duties as necessary
- Employee salaries
- Initial costs for a pick and pack warehouse management system software, including recurring monthly or annual fees
- Hiring a person or a system to keep the warehouse organized
- Keeping inventory continually and consistently updated
- Boxes, bags, cartons, pallets, totes, and other shipping options
- Package labels
- Quality control measures
- Box sealing
Ultimately, business owners often try cutting down on shipping costs as much as possible when it comes to final fees. Interested in cheap transportation fees? Learn more about economy shipping.
In addition, check out our guide on the difference between shipping and delivery!
7. Greater Customer Satisfaction
Third-party logistics pick and pack services can increase delivery speed, order accuracy, and overall customer satisfaction. A pick and pack system allows for customers to receive their correct orders in a short amount of time, which will certainly boost customer loyalty.
Which Pick and Pack Fulfillment Process Is Right for Your Business?
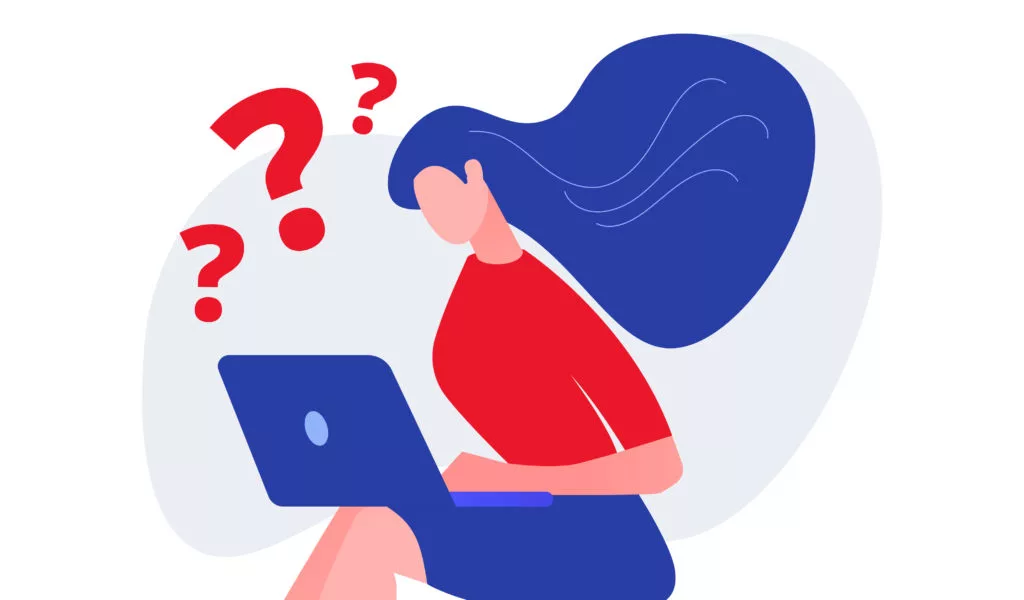
Common types of order picking methods include:
- Discrete order picking
- Batch picking
- Wave picking
- Zone picking
- Technology-based picking
1. Discrete Order Picking
This is the most common method of order picking.
Discrete picking is when a picker goes through each order one at a time, grabbing an object line by line. Many companies that use discrete picking have low order volumes or large/heavy products.
The time it takes for someone to walk around and pick the items that customers have ordered is the main reason why orders can’t be processed quickly when there are many of them.
2. Batch Picking
If you have a lot of orders to pick, batch picking is an excellent way to do it. This is when you group all the orders for products in the same area in the warehouse. Batch picking will help make sure the pickers can go through the warehouse most effectively.
When you need an item for multiple orders, it makes sense to select all those orders simultaneously. This way, you won’t have to walk back and forth between the different areas. Your orders will be processed more quickly that way.
Even if your company is small, you can use batch picking. This means that you pick up all your orders in one day instead of picking and packing them as they come in. You can do this by choosing all of your orders at once. Picking software can help you batch orders more effectively.
3. Wave Picking
Wave picking is when you pick several orders at the same time. This is done by taking two invoices from the printer at the same time and getting the supplies for each order at the same time. This way, you won’t have to go back and forth across the warehouse twice.
4. Zone Picking
In warehouse management and supply chain logistics, zone picking is a way to pick orders. This is done by dividing stock-keeping units into different zones. Employees will choose and sort from within their zone.
Some warehouses have different zones for picking things. People or machines can pick things in these zones. For example, a warehouse that sells electrical products might have a zone for picking big and heavy items with a powered pallet truck. Another zone will be for picking lighter items with someone’s hands.
These two items need to be combined, but they will be done by moving them to the same zone or the sorting and packaging area.
5. Technology-Based Picking Methods
Voice technology and mobile picking are two of the most significant technological advancements for order pickers.
Voice-Assisted Picking
The microphone headset worn by your pickers is the most important piece of equipment. They will listen to directions about where to go and what to choose.
Mobile Order Picking
If all your products have unique barcodes, a mobile scanning technology may be a good match for your warehouse. A WMS can send picking details and the best picking path to your pickers’ mobile devices. This will help them pick the product quickly and easily.
Types of Pick and Pack Warehousing Setups
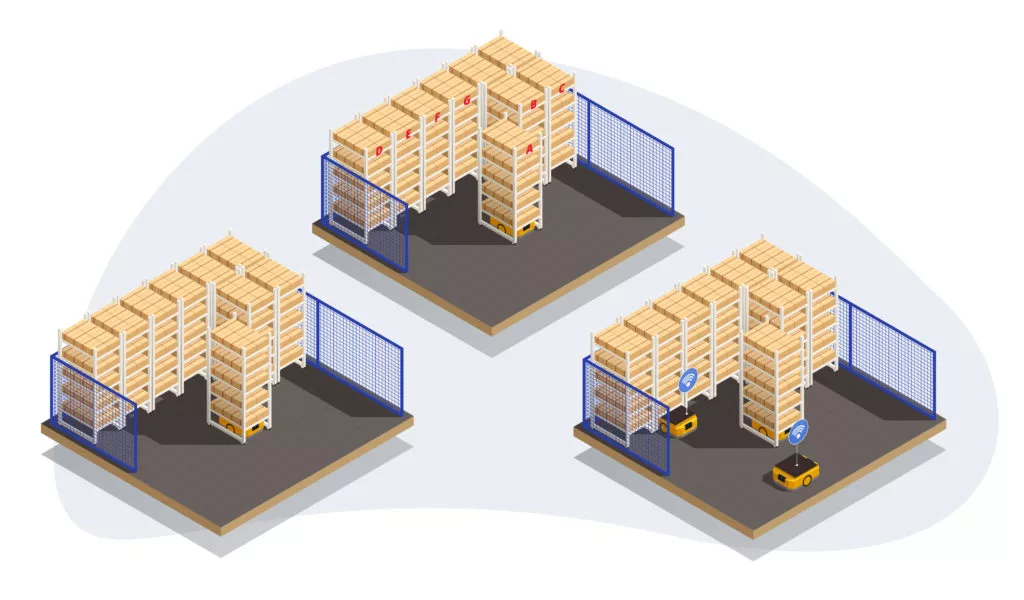
Organizing your warehouse differently will help your pick and pack methods work better.
1. Chaotic Inventory Management
In chaotic inventory management systems, you place your products randomly on the shelves. This way, a product will never be next to a similar outcome. Your error rate will go way down.
To make chaotic inventory storage work, you need inventory management software. This software will map the products in your warehouse. When you print a packing slip, each item will have a location. Some software can also map the most efficient route through your warehouse so you can pick orders more quickly.
2. Volume and Class-Based Inventory Management
There are two more types of inventory storage. You can use a chaotic approach to inventory management. This means you put the SKUs with the highest turnover closest to the packing station. Products that sell the slowest are stored in the farthest location. This way, pickers take fewer steps during the day to pick orders.
Another inventory storage system is class-based. Items are grouped together into classes based on a shared trait. This can be the turnover rate of the products, how they are packed, or if they need an over box.
3. Mobile Shelf-Based Order Pick Systems
One way to pick and pack products is using mobile shelf-based order pick systems or MSOP. In this system, robots bring shelves of products to the picker. The picker stays stationary while the robots shuttle the shelves back and forth.
What Is Pick and Pack Software?
Order picking software helps optimize and improve the process of picking and packing orders in a warehouse. This type of software can help streamline fulfillment operations, leading to increased order accuracy and a better overall customer experience.
How Pick and Pack Software Can Optimize the Fulfillment Process
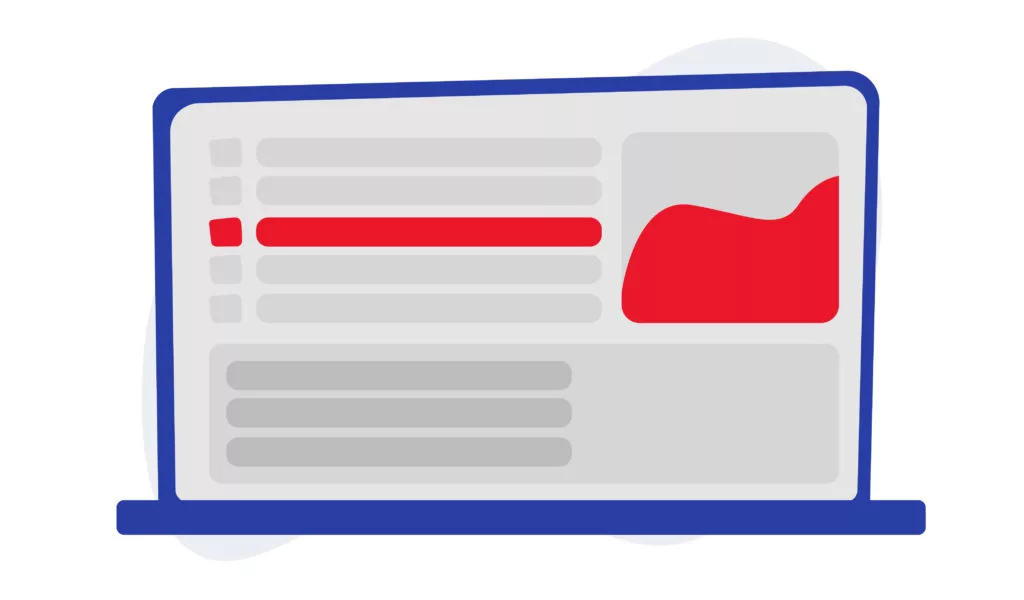
In any logistics operation, total optimization is the end goal. Consider learning more about implementing logistics optimization successfully.
Here are a few ways pick and pack software can help optimize your fulfillment process.
1. Higher Accuracy in Packing Orders
Most order errors happen during the picking and packing phase. This is where pick and pack software can help you. Pick and pack software helps maintain a high order accuracy rate for all orders being fulfilled. It also makes the picker’s process easier and more efficient, which can boost warehouse productivity.
2. Lower Costs for Warehouse Operations
The warehouse picking process is expensive because it is very labor-intensive. This is especially true in larger warehouses. However, pick and pack software can help to reduce costs by reducing the amount of manual labor needed and increasing productivity. Using a pick and pack software, you can save money on labor costs for the order fulfillment process.
Pick and pack software helps you keep track of customer orders. This will make the order picking process more accurate and efficient, saving time and money.
3. Greater Customer Satisfaction
If you have the right pick and pack software, your customers will be happy with their orders. The software will make sure that the items are packed and shipped correctly. This can affect customer satisfaction because it can mean the difference between a delivery arriving on time and accurately or one with missing or incorrect items.
4. Better Internal Communications
Pick and pack software can help improve internal communications by allowing your team to work together to optimize the picking and packing process.
If your warehouse is organized in a way that reduces human error, your employees will have time to come up with new ideas for improving the process.
Notable Pick and Pack Software Solutions
1. Stitch Labs
Stitch Labs is a company that designs software to help businesses sell things online. The software can help you manage your inventory, shipping, and how you deliver the products to the customers.
2. Skubana
Skubana offers software that helps eCommerce businesses manage their orders, inventory, and analytics.
Why E-Commerce Businesses Are Turning to Third-Party Logistics for Pick and Pack Systems
3PLs offer a valuable service that is in high demand. These shipping and fulfillment experts store your inventory in their warehouses and then pick, pack, and ship products to your customers.
That’s why so many Fortune 500 companies turn to third-party logistics providers. The market for 3PLs has grown a lot in recent years and is predicted to be worth trillions of dollars by 2026.
If you think your business might grow a lot, it’s a good idea to choose a 3PL before you get too overwhelmed. A 3PL is for any size business that wants to grow. So if you have a flash sale or one of your products becomes popular, it’s not always easy to handle all the extra orders yourself.
If you are fulfilling more than 10 to 20 orders daily, calculate the costs of partnering with a 3PL to keep your profit margins strong. Outsourcing packing, picking, and shipping can save time on manual labor.
In addition, merchants often forget to include storage costs in their fulfillment expense calculations. This can be a big mistake because 21% of a company’s logistical costs are spent on inventory carrying.
When deciding if a 3PL is right for your online business, compare your current warehouse expenses to the estimates from 3PLs. Sometimes, if you bundle storage costs with outsourced fulfillment, you will get better value for your money.
Pick and Pack Companies
Here are a few notable companies that can help provide you with a pick and pack system solution:
- USA Fulfillment – USA Fulfillment helps companies manage their supply chains.
- Dropoff – Dropoff offers custom logistics services and nationwide coverage to support any business.
- Invenco – Invenco is dedicated to helping your online business succeed.
- FW Logistics – FW Logistics can help business owners meet their logistics goals.
- Red Stag Fulfillment – Red Stag Fulfillment takes care of your product shipping securely.
Further, if you want to partner with a third-party logistics company, check out our top picks of the best last-mile delivery companies and startups in the US.
Bottom Line
Online businesses love pick and pack systems because they make the order fulfillment process more efficient. E-commerce businesses can save time and money by streamlining the picking and packing process.
Talk with a Dropoff expert today if you’re looking for a way to improve your order fulfillment process. We can help you find the right system for your business.
FAQs – Pick and Pack Logistics
1. What does pick and pack mean?
Pick and pack is a job where you have to choose the right type and number of items from shelves and put them in packages so they can be shipped.
2. What are pick and pack fees?
The pick and pack fee is what you pay to have an item or items picked from storage and packaged for shipping. This fee usually costs between $3 and $5 per item. Some companies offer bulk rates if you are shipping multiple items, but some may also charge a small order fee.
3. What is the best working zone for picking and packing?
The workplace should be designed so that operatives can easily pick up the things they need from working zones between their shoulders and knees.