The Advantages and Disadvantages of Reverse Logistics
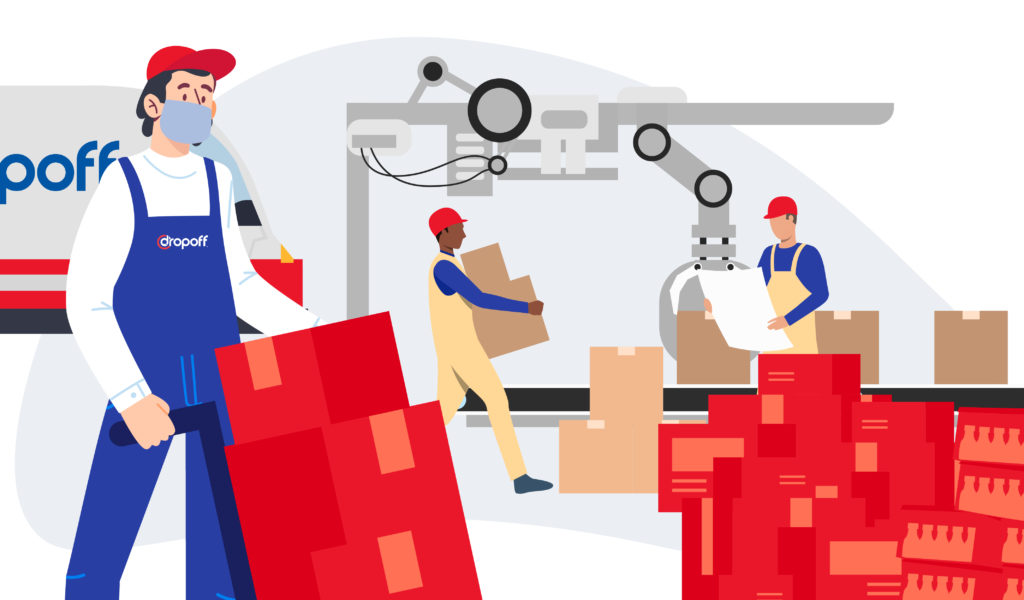
What is reverse logistics? In a nutshell, it’s moving goods backward through the supply chain. The process includes returning products to suppliers, redistributing products to retailers or consumers, or recycling and disposing of products.
In this blog post, we’ll discuss the advantages and disadvantages of reverse logistics to help you make an informed decision about how you can optimize it in your business.
What Is Reverse Logistics?
Reverse logistics is a supply chain process that moves goods from customers back to the sellers or manufacturers. It occurs when a customer has received a product and needs to return or recycle it.
It starts with the end consumer who buys the product. The process goes backward through the supply chain to the distributor or from the distributor to the manufacturer.
Advantages and Disadvantages of Reverse Logistics
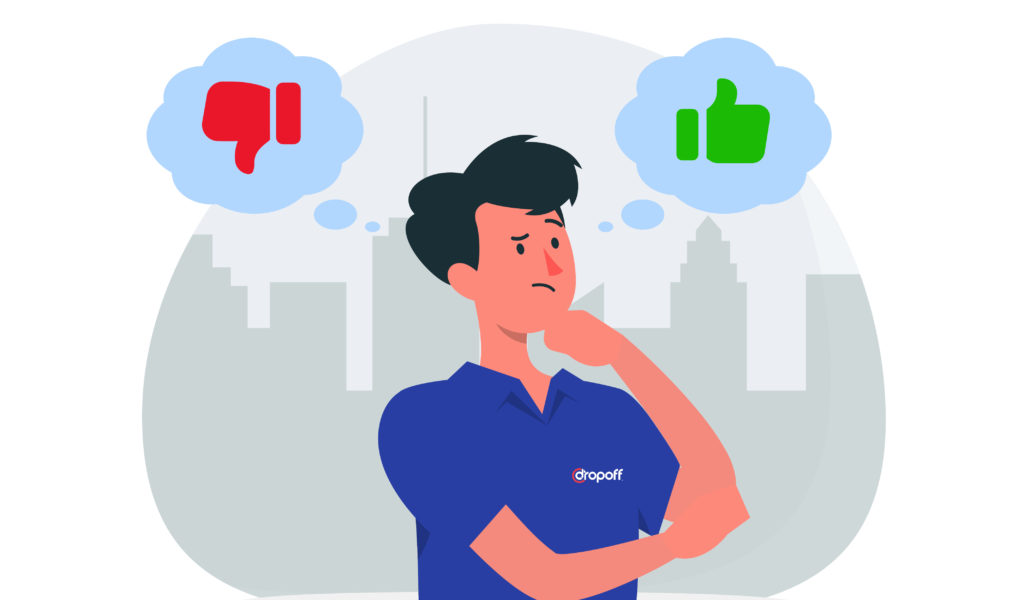
There are some clear advantages and disadvantages associated with reverse logistics.
Advantages of Reverse Logistics
When done correctly, reverse logistics helps to reduce waste, improve customer satisfaction, and generate new revenue streams.
Let’s take a closer look at the benefits of an efficient reverse logistics process.
1. Lower Costs
One of the many pros of reverse logistics includes cutting down on costs.
A well-run reverse logistics system helps your business save money. For example, you could save on administration, repairs, tech support, quality assurance, marketing, and disposal costs. It is also possible to save on transportation by offering economy shipping.
2. Higher Customer Satisfaction
Focusing on customer retention is one of the best ways to meet your business goals. It is much harder to attract new customers than to keep the ones you already have.
Here are some services to offer customers to improve their return experience:
- Provide free shipping for return items
- Issue customers a full refund
- Customers are not required to send back the original packaging
3. Stronger Brand Reputation
Customers care about how you handle returns. They will not purchase from you if you do not have a friendly return policy. If your business is known for being difficult when customers want or need to return something, it will appear in reviews and ultimately hurt your business’s reputation.
4. Lower Risk Management
A reverse logistics process is vital for businesses as it helps protect them from any risks associated with product exchanges and disposal. For example, some products need to undergo disposal immediately due to a safety recall. Others contain confidential data that must be deleted before recycling or disposal.
5. Improved Sustainability
Some people think everything that comes back through the reverse logistics supply chain is garbage and ready for disposal. But that’s not always the case. Some items must be disposed of properly, but many items come back intact. If we reuse these items, we keep them out of the landfill for longer.
You should also offer to recycle certain items, like electronics, to have less of an environmental impact.
6. Improved Profitability
Remember that many returned products are simply not the right size, color, or model number for them. The items are usually in good condition and can be sold again.
If something goes wrong with a product and the customer wants to return it, a well-oiled reverse logistics process will help make the process as smooth as possible. Receiving the product at a staging area, inspecting it, making any necessary repairs, and putting it into refurbished inventory for sale.
Further, learn more about optimizing your reverse logistics process through our guide on logistics optimization.
Disadvantages of Reverse Logistics
While reverse logistics offers many advantages for businesses, there are also some potential disadvantages.
1. Complicated Return Order Flows
Reverse supply chains involve coordinating multiple business partners and points of origin to get products back to where they need to go.
Once a product reaches a Central Distribution Center (CDC) or Returns Forwarding Center (RFC), several steps are involved in receiving and handling a return, including:
- Verifying the product
- Inspecting the product
- Testing the product
- Determining whether it would be more cost-effective to dispose of or recycle raw materials instead of refurbishing the product
- Completing any product repairs
- Repackaging the product to be placed in refurbished inventory
It is often challenging for manufacturers to keep track of the information between different parts of the company and to track orders.
2. Return Merchandise Authorization (RMA)
To prevent revenue loss, the person approving returns should determine why the customer is returning the product. If the problem can be fixed on the spot, the vendor should provide a solution for the customer and persuade them not to return the product they bought.
You must record information about the entitlements, service level expectations, and order constraints if the return is authorized.
3. Changing Customer Demands
Customers who buy products for businesses or themselves expect to get the same services they would get if they were buying in person. They want to see how much stock is left how fast the delivery is, and how easy it is to return any items.
Companies are motivated to improve their returns management systems to keep up with customer demand and stay competitive.
4. Lack of Customer Knowledge
It is an excellent idea to provide customers with detailed catalogs and identification guides. They will make more informed purchases and use your products correctly, decreasing the number of returns on products.
5. Meeting the Rising Demand
Since the pandemic started, people have been using more electronics at home. As a result, they need more repair services. To meet this demand, manufacturers have been updating their processes so that repairs are faster.
In relation to managing high-demand orders, learn how to manage on-demand logistics in your business.
6. Lower Waste and Carbon Emission
Organizations trying to reduce carbon emissions and waste have more options than ever to make their supply chain more sustainable.
Manufacturers reduce the number of new materials they need by using green strategies in the reverse supply chain. Doing so makes it easier for them to follow government mandates and environmental regulations.
Reverse Logistics Examples in Real Businesses
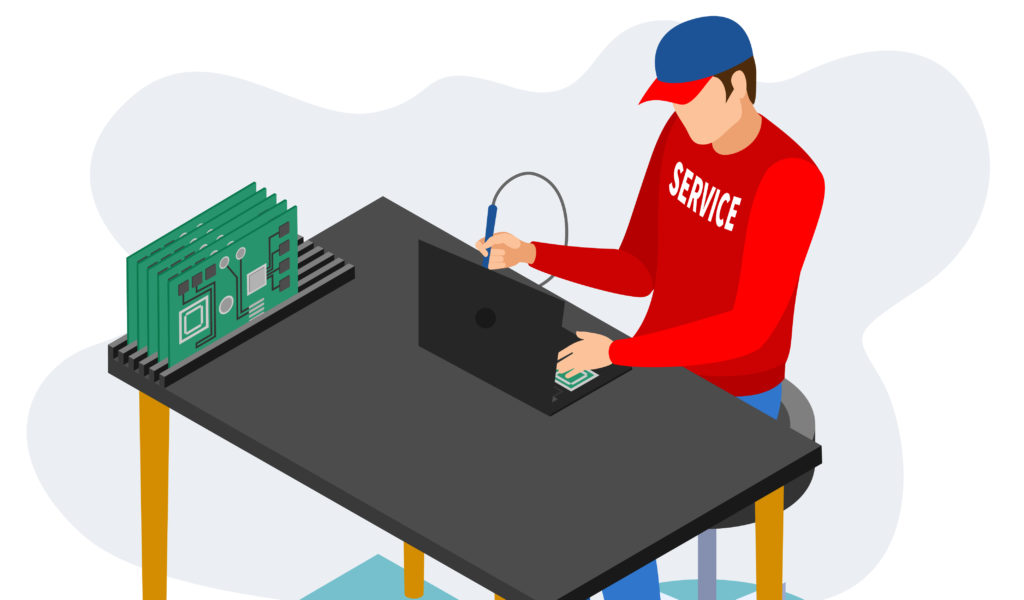
Here are a few concrete examples of how good reverse logistics management has helped businesses:
1. Product Refurbishment – Rent the Runway
Refurbishment is fixing and reselling if a customer brings back a product. The product must not have too much damage from the previous customer and must undergo a reconditioning process.
At Rent the Runway, refurbishment is a common practice. It is part of their business model to offer pieces rented from 550 designers on their website.
The company’s warehouse needs good organization so that it’s ready to receive items that customers return, clean them, and store them until another customer rents them in the future.
2. Product Repair – Cosgra
Fixing damaged products means making them work again. Often, it involves replacing a part that has worn out or stopped working.
Cosgra, a distributor for automotive and electronics businesses, has a warehouse that stores products sold in over 20 countries in Europe, Africa, and Latin America. Additionally, they have a space set up for repairs that companies use all over the world.
The company uses a WMS from the Mecalux Group to organize returns and repairs. This system tells operators what to do at every step, including where to store the product on the pallet racks or how to repair it to extend its life.
3 Reasons Why 3PLs Make Reverse Logistics Easier
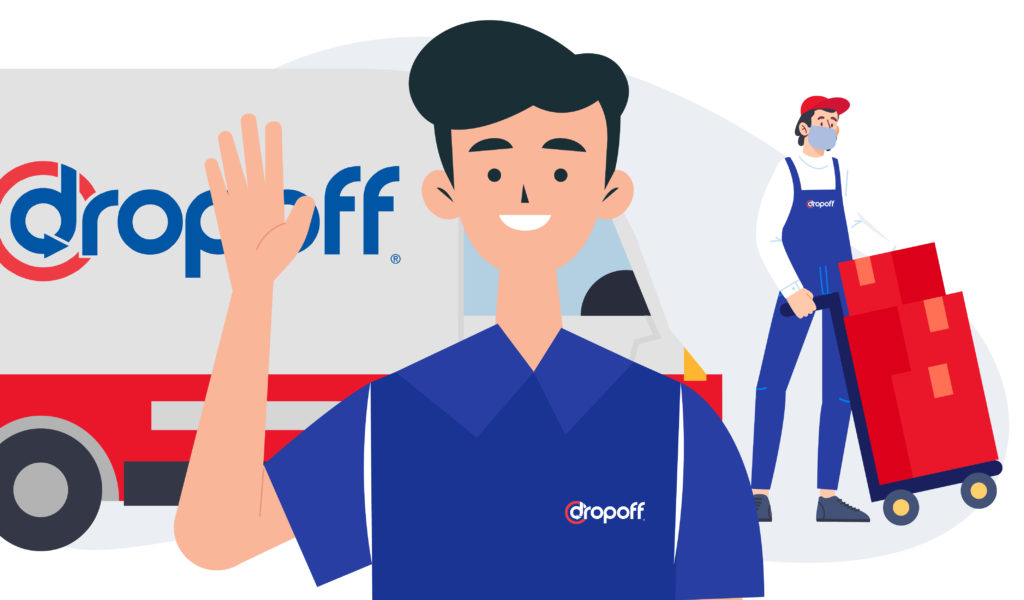
3PLs like Dropoff are known for their flexibility and scalability. These traits are essential for e-commerce today because they help businesses save money and stay organized.
In addition, 3PLs are experts at managing different logistics processes, including omnichannel logistics.
Here are a few ways outsourcing reverse logistics functions can benefit your business:
1. Higher Customer Retention
3PLs are known for having long-term customer relationships. The longevity of these relationships is based on trust. Because transparency into shipping operations is so important to buyers today, you and your customers must be able to trust the reliability of your shipper.
2. Increased Revenue
If a business provides quick and easy shipping, it will become someone’s go-to retailer. When a 3PL is transparent and reliable, customers won’t have any complaints about the shipping process.
Check out our article on the difference between shipping and delivery!
3. Product Improvement
Couriers like Dropoff use software that helps them deliver products more quickly and efficiently. It collects data and offers advanced analytics, that helps identify quality control issues. By analyzing return data, you get a better understanding of the types of products that are returned and why.
3PLs aren’t just great at reverse logistics; they manage door-to-door delivery excellently too.
Bottom Line
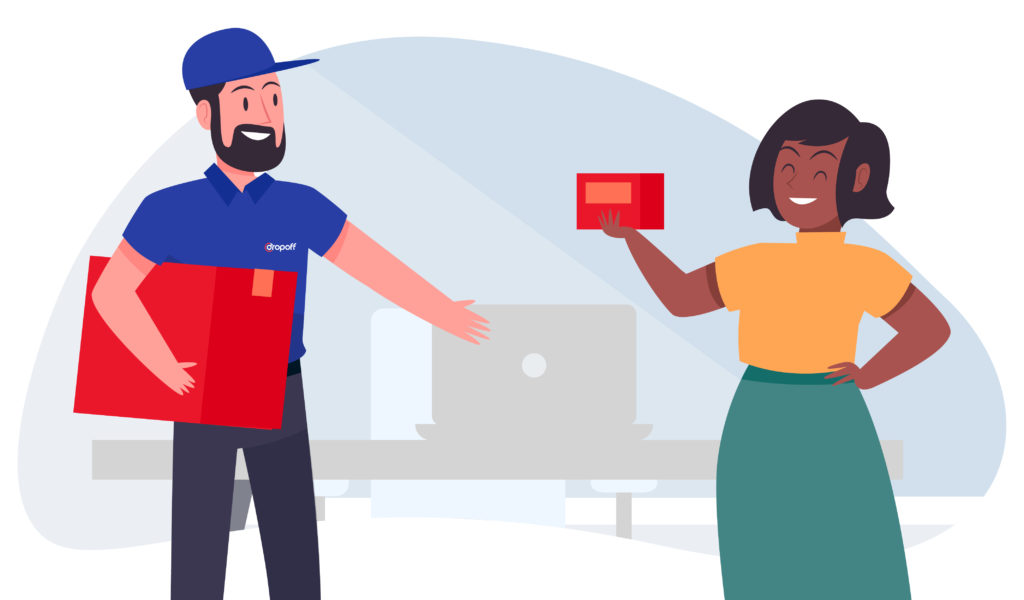
Reverse logistics is a great way to improve your customer service and decrease the amount of product you have to dispose of, but it’s not always perfect. The advantages and disadvantages of reverse logistics discussed in this article should give you a clearer picture of the entire operation.
If you’re looking for a reverse logistics partner, Dropoff is here to help.
Talk with a Dropoff expert today about streamlining your reverse logistics operation and making it more efficient.
FAQs on Reverse Logistics
1. What is reverse logistics in the supply chain?
Reverse logistics is a type of supply chain management that moves goods from customers back to the sellers or manufacturers. It occurs when a customer has received a product and needs to return or recycle it.
2. When is reverse logistics used?
Organizations use reverse logistics when items move from the seller back through the supply chain to the originator and perhaps back to suppliers. The objective is to reclaim money from the goods or dispose of them. Every year, worldwide returns amount to over a trillion dollars, which has risen with e-commerce’s expansion.
3. What are the 5 Rs of reverse logistics?
The five Rs of reverse logistics are returns, reselling, repairs, replacements, and recycling.