Warehouse Control System: Everything To Know About in 2024
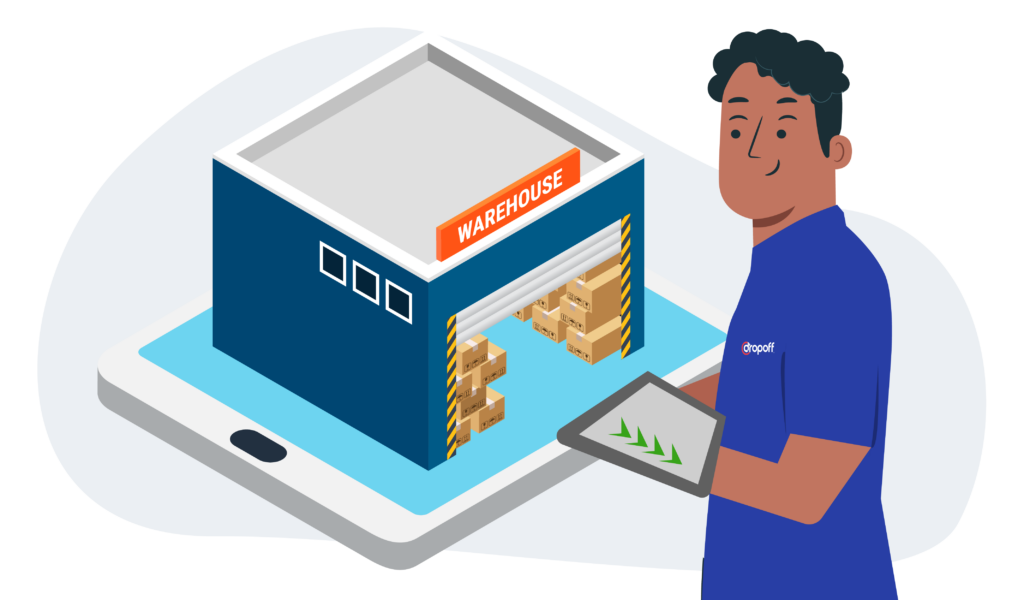
Shifting vacant spaces into warehouses has been a popular business idea, not just for supply chain companies but even for private individuals. Surprisingly, though, all these efforts are still not enough, and numerous businesses are still having a hard time managing their warehouses.
Why? Because there’s more to a supply chain than mere warehouses, you must have a great warehouse control system to prevent storage and handling issues for your business.
This article delves into the core aspects of WCS, shedding light on its definition and key components, differentiating it from WES and WMS, and identifying signs of a high-quality WCS system. Additionally, we will explore the challenges inherent in implementing WCS, offer insights into initiating your journey with WCS, and look at how Dropoff can be your ally in this transformative process.
What is a WCS or Warehouse Control System?
In the face of rising eCommerce demands and a shortage of warehouse space, logistics companies are implementing strategic measures to address storage capacity challenges. Proactive steps include securing agreements for new storage facilities well before construction begins and expanding searches for locations beyond coastal ports, such as Knoxville, Tenn.; the Lehigh Valley in Pennsylvania; and Reno, Nev.
Alongside these efforts, the industry is turning to technological solutions, with Warehouse Control Systems (WCS) emerging as a key tool.
A Warehouse Control System (WCS) is sophisticated software designed to orchestrate, manage, and optimize activities within a warehouse or distribution center. As the operational nerve center, WCS facilitates seamless coordination among various material handling subsystems, directing the flow of products, maximizing the efficiency of automated equipment, and, at times, even generating insights for last-mile deliveries.
To delve deeper into warehouse management, it’s crucial to distinguish between WES, WCS, and WMS solutions.
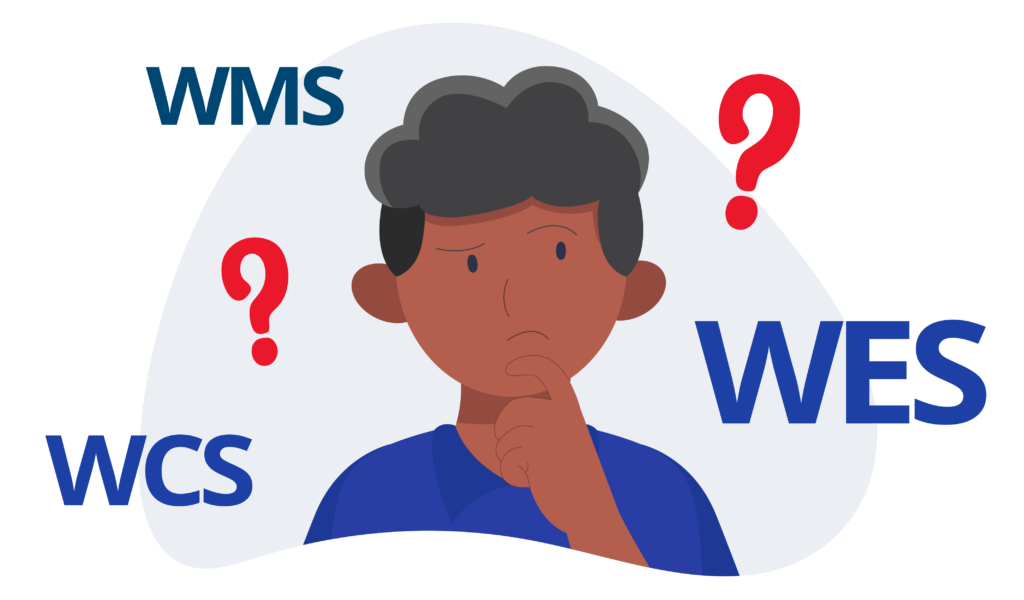
What is the Difference Between WES, WCS, and WMS?
To comprehend WCS solutions better, it’s vital to grasp the nuances between a Warehouse Execution System (WES), Warehouse Control System (WCS), and Warehouse Management System (WMS).
Warehouse Execution System (WES)
As a comprehensive solution, WES integrates features from both WCS and WMS. It optimizes tasks and equipment functions in automated warehouses, providing real-time inputs for dynamic and adaptive work processes. WES oversees the execution process, fostering efficient collaboration between warehouse components for heightened productivity in automated environments.
Warehouse Control System (WCS)
Dedicated to real-time control and optimization of Material Handling Equipment (MHE), WCS acts as orchestrator of warehouse activities. It ensures seamless communication between systems and devices, emphasizing tasks like order fulfillment management, inventory control, and equipment coordination. While offering real-time control, WCS typically doesn’t handle broader operational management functions, leaving tasks like labor management to other systems.
Warehouse Management System (WMS)
WMS operates at a broader level and encompasses various warehouse management functions, focusing on overall operations and task prioritization. It deals with inventory management, order processing, slotting optimization, and warehouse organization. Unlike WCS and WES, WMS doesn’t involve real-time control of material handling equipment but concentrates on strategic decision-making, ensuring accurate inventory tracking, efficient order processing, and optimal warehouse operation.
Return of Investment for Warehouse Control Systems
Warehouse Control Systems (WCS) yield significant impacts, boasting a 25% surge in productivity, a notable 20% reduction in space consumption, and a commendable 30% enhancement in stock efficiency.
These improvements result from streamlined workflows, heightened order accuracy, and effective labor management, all facilitated by Warehouse Management Systems (WMS). WMS is pivotal in optimizing inventory placement and storage organization, contributing to cost savings and operational enhancements and showcasing its undeniable benefits.
However, businesses considering WMS implementation, with costs ranging from $5,000 per year and beyond, must thoroughly evaluate the Return on Investment (ROI). This involves a meticulous comparison between the monthly cost of WMS implementation (e.g., $2,000) and the tangible monthly savings derived from increased productivity, optimized space utilization, and improved stock efficiency. The breakeven point, indicating when monthly savings surpass the monthly cost, becomes a critical indicator, signaling the point at which the investment in WMS becomes financially advantageous for the business.
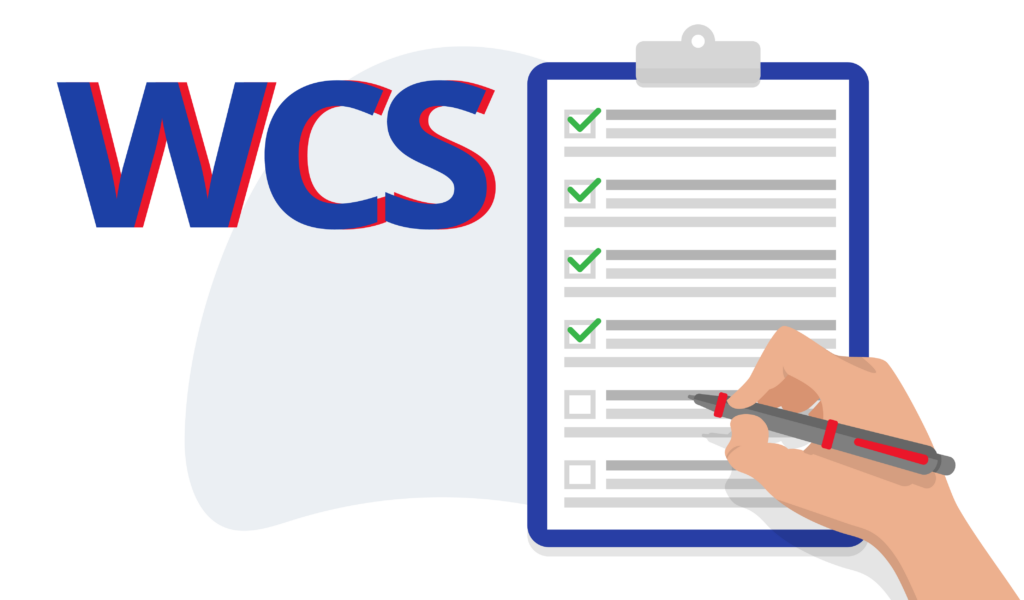
7 Key Components of a Warehouse Control System
A Warehouse Control System (WCS) is a critical component of modern warehouse management, providing real-time control and optimization of various tasks and processes. The key components of a Warehouse Control System software include:
1. Material Handling Equipment (MHE) Integration
Logistics experts suggest that an efficient MHE integration can help businesses increase their revenue generation by up to 50%. For WCS, this includes:
- Conveyor Systems: WCS integrates with conveyor systems to optimize the flow of goods through the warehouse. It ensures that conveyor routes are efficiently utilized.
- Automated Guided Vehicles (AGVs): WCS communicates with AGVs to orchestrate their movement, ensuring they follow optimal paths and coordinate with other equipment and warehouse activities.
2. Order Fulfillment Management
The fees for outsourced warehouse fulfillment services usually run up to $5 per package. This cost alone can cost millions for businesses, so an efficient automated WCS system should involve:
- Order Processing: WCS manages and optimizes the order fulfillment process, ensuring accurate and timely picking, packing, and shipping of orders.
- Wave Planning: It organizes and plans order waves to maximize efficiency in picking and packing operations, reducing the overall order cycle time.
3. Inventory Management
A typical inventory management solution usually charges from $10,000 to $40,000 for a 12-16 week rollout. To maximize this, your delivery management solution should include:
- Real-time Inventory Visibility: WCS provides real-time visibility into inventory levels, ensuring accurate tracking of stock levels and preventing stock-outs or overstocks.
- Slotting Optimization: It optimizes the placement of products within the warehouse, considering factors such as picking frequency, product characteristics, and storage constraints.
4. Labor Management
The cost of labor can account for up to 65% of total warehouse fulfillment costs, excluding trucking, depending on the operations. A WCS solution ensures that you efficiently manage your staff by including the following services:
- Task Assignment: WCS assigns tasks to warehouse staff based on priorities, order deadlines, and individual worker efficiency, ensuring optimal use of labor resources.
- Performance Monitoring: It monitors the performance of warehouse staff, providing insights into productivity efficiency and identifying areas for improvement.
5. System Integration
A study by the Boston Consulting Group revealed that businesses with integrated systems have seen a 40% improvement in their operations. With this in mind, it’s imperative for your WCS software to be fully integrated into your infrastructure, specifically on the following terms:
- Enterprise Resource Planning (ERP) Integration: Streamlining communication between the WCS and critical business processes like order processing, procurement, and financials ensures cohesive operations and data synchronization.
- Warehouse Management System (WMS) Integration: This enables a synchronized approach to warehouse processes, leveraging the strategic functionalities of WMS alongside the real-time control and optimization capabilities of WCS.
6. Task Scheduling and Dispatching
Task scheduling and dispatching are often facilitated manually, which consumes 50% of logistics workers’ time. It’s imperative to have these automated services to ensure seamless operations:
- Dynamic Task Scheduling: WCS dynamically schedules and dispatches tasks to various warehouse resources, optimizing the flow of work and preventing congestion.
- Resource Allocation: It allocates resources efficiently, considering factors like equipment availability, order priorities, and warehouse layout.
7. Reporting and Analytics
According to Forbes, 59% of businesses now use data analytics in their operations, including on their supply chain. WCS systems should be able to generate the following:
- Performance Metrics: WCS provides detailed analytics and reporting on warehouse performance, allowing managers to assess efficiency, identify bottlenecks, and make data-driven improvements.
- KPI Monitoring: Key Performance Indicators (KPIs) related to order fulfillment, inventory accuracy, and labor productivity are monitored and reported for continuous improvement.
5 Signs of a High-Quality WCS Solutions
There are now numerous WCS providers in the market today. Despite this, not all automated warehouse control systems can help your business fulfill its goals. Here are the top factors you should consider when looking for Warehouse Control Systems:
- Integration with Automation Technologies
A prime example of a high-quality WCS system showcasing seamless integration with automation technologies is seen in Amazon’s fulfillment centers.
Amazon utilizes advanced conveyor systems, robotics, and sorting mechanisms, all orchestrated by a robust WCS. The system ensures a harmonious workflow, optimizing the movement of products through the automated warehouse environment. The best part is this WCS software is accessible by all Amazon partners.
- Real-Time Monitoring and Reporting
DHL Supply Chain is an exemplary case of a company implementing a high-quality WCS system with real-time monitoring and reporting capabilities.
DHL’s WCS provides instant visibility into warehouse operations, allowing for proactive decision-making. The system’s monitoring and reporting tools contribute to efficient management by providing actionable insights into various facets of the supply chain.
- Reliable Error Handling and Recovery
Companies like Zalando rely on a top-notch WCS for reliable error handling and recovery. Zalando’s WCS minimizes downtime by swiftly identifying and rectifying errors, ensuring a continuous and uninterrupted flow of operations within their fulfillment centers.
- Scalability and Flexibility
The scalability and flexibility of a quality WCS are demonstrated by the implementation at Alibaba’s warehouses.
Alibaba’s business growth demands a system that can adapt to changing needs and expanding volumes. Their WCS facilitates this scalability, ensuring the smooth handling of an ever-increasing volume of orders. The company was able to accommodate numerous dropshipping accounts, all integrated into their efficiently managed warehouse.
- User-Friendly Interface
An illustrative example of a WCS with a user-friendly interface is found in the logistics operations of FedEx. FedEx’s WCS, named as FORT solutions, offers warehouse personnel a straightforward and intuitive interface, reducing the learning curve. This user-friendly design enhances efficiency and allows staff to navigate the system seamlessly.
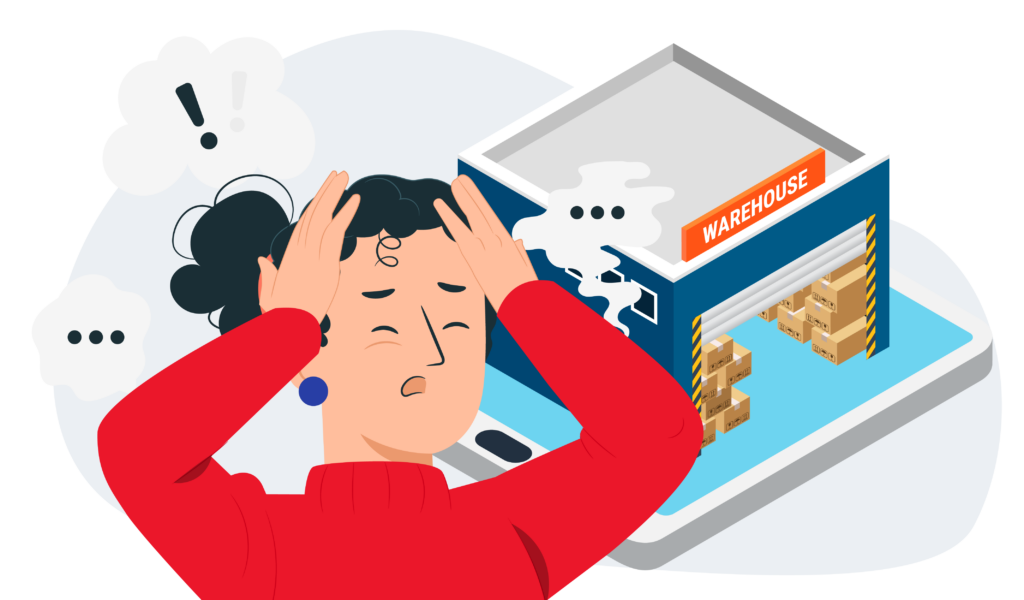
5 Challenges of Implementing WCS
While the benefits of an efficient WCS solution are undeniable, implementing such has a steep learning curve, especially for SMEs. To help you with this, here are the five challenges you should prepare for:
Integration Complexity
The integration complexity of WCS is evident in the experiences of companies like Walmart.
Walmart faced challenges when integrating WCS with existing systems, especially in terms of moving slow-selling items. Because of this, in 2021, they implemented an omnichannel strategy that allowed them to expand their eCommerce assortment while reducing shipping time and cost.
Data Accuracy
Maintaining data accuracy and safety is critical, as data mismanagement is one of the most common warehouse mistakes among logistics providers. Inaccuracies in data can lead to operational disruptions and impact decision-making, rendering an entire supply chain useless.
Employee Readiness for Innovation
Companies such as Coca-Cola have encountered challenges related to employee readiness for technological innovations in their logistics management, specifically in their American and East Asian units.
As exemplified by the brand, overcoming resistance to change among employees requires adequate training and fostering a culture of innovation to ensure a smooth transition to the new system.
Customization
The need for customization in WCS is exemplified by the experiences of companies like Procter & Gamble (P&G). Instead of going for traditional WCS operations, the company partnered with SAP to optimize its operations for its clientele.
The company opted to replace the three legacy logistics operations: handling, storage, and transport to streamline a better warehouse and packing process. Companies implementing WCS for the first time should understand how to customize their solutions.
ROI Calculation
Calculating the ROI for WCS implementation involves strategic planning, as evidenced by the experiences of companies like UPS.
To help eCommerce brands and SMEs, there are now numerous third-party software that help businesses calculate the cost of their UPS shipments. A clear understanding of the metrics and long-term benefits is essential for UPS to justify the investment in WCS effectively.
It’s Time to Start Working with WCS: Your First Steps
When venturing into the Warehouse Control System (WCS) implementation, it’s crucial to adopt a strategic and methodical approach.
Commence your WCS journey by conducting a thorough assessment of your warehouse’s distinctive needs and operational dynamics. This initial step involves close collaboration with both your operations and IT teams to ensure a holistic understanding of the existing processes, technological infrastructure, financial considerations, and scheduling requirements.
After this, define clear and achievable goals of your WCS solution. Work closely with key stakeholders to establish well-defined objectives that align with your warehouse’s unique demands and overarching business objectives. These goals should encompass various aspects, such as optimizing order fulfillment processes, enhancing inventory control, and improving overall warehouse efficiency.
Lastly, ensure collaborative effort between operations and IT teams and prioritize features within the WCS that directly align with your warehouse’s specific requirements. By aligning technological capabilities with operational needs, you ensure that the selected WCS solution not only meets the immediate demands of your warehouse but also lays the foundation for scalable, adaptable, and efficient logistics operations.
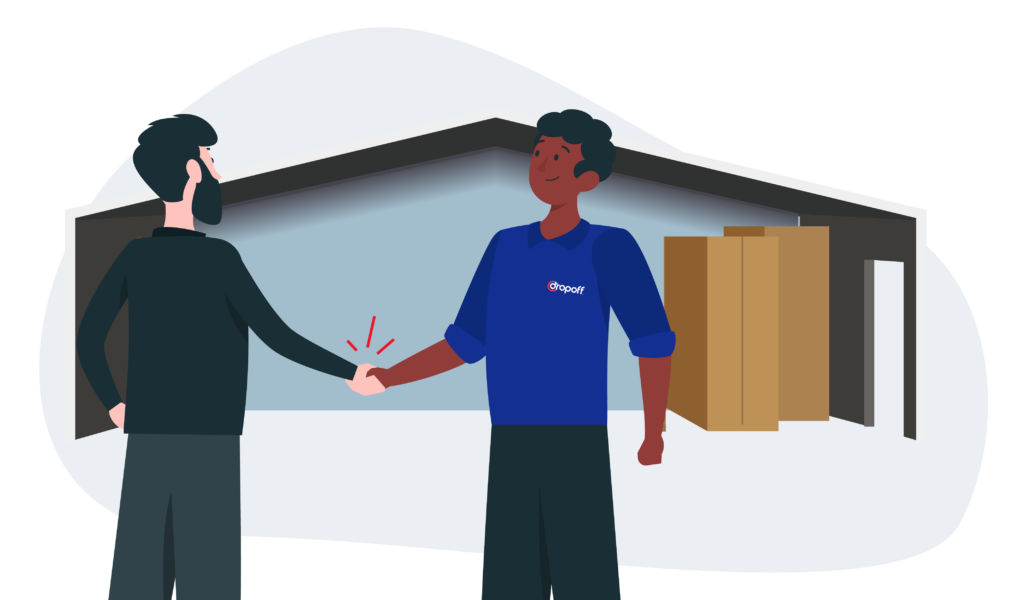
How Dropoff Can Help You with the WCS
Renowned for its leadership in logistics and warehouse solutions, Dropoff emerges as a crucial ally in WCS implementation. Through close collaboration with client organizations, Dropoff ensures the seamless integration of a company’s WCS to their last-mile deliveries, providing indispensable tools to expedite the supply chain process and optimize overall operational efficiency.
What distinguishes Dropoff is state-of-the-art logistics software, offering full-scale delivery automation, real-time tracking, and image confirmations. Most importantly, the company provides personalized same-day delivery services crafted to meet the distinctive needs of each client. This commitment extends to a steadfast assurance of guaranteed on-time delivery, supported by transparent courier actions.
FAQs:
A WCS is sophisticated software that orchestrates, manages, and optimizes warehouse activities, ensuring seamless coordination among material handling subsystems.
WCS focuses on real-time control and optimization of Material Handling Equipment (MHE), distinguishing it from Warehouse Execution System (WES) and Warehouse Management System (WMS).
Key components include MHE Integration, Order Fulfillment Management, Inventory Management, Labor Management, System Integration, Task Scheduling and Dispatching, and Reporting and Analytics.
On average, WCS yields a 25% increase in productivity, a 20% reduction in space consumption, and a 30% improvement in stock efficiency, contributing to a positive ROI through increased productivity and operational enhancements.
Challenges include integration complexity, data accuracy concerns, employee readiness for innovation, customization needs, and the importance of careful ROI calculation for a successful implementation.