7 Main Warehouse Shipping Mistakes and How to Avoid Them

When shipping products, it’s important to consider some factors to avoid common mistakes. These mistakes without a doubt lead to lower sales and poor customer satisfaction.
In this blog post, we’ll take a closer look at some of the most common warehouse shipping mistakes and how to avoid them.
What Is Warehouse Shipping?
Warehouse shipping is transporting items from a warehouse to the customer’s doorstep. There are two types of shipping for warehouses: small parcel shipping and freight shipping.
How Does Warehouse Shipping Work?
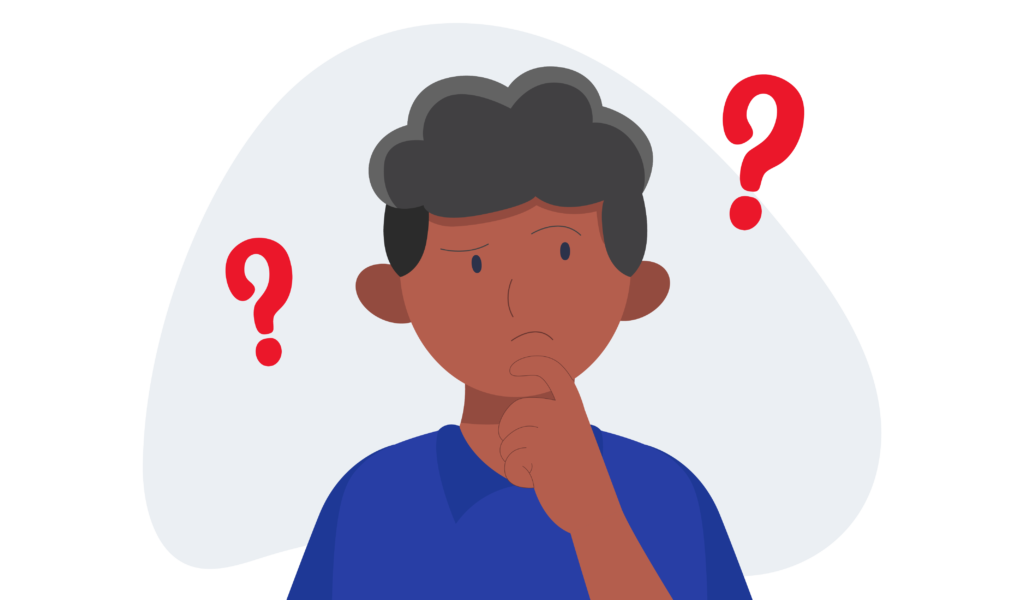
There are three stages of the warehouse shipping process:
- Create and manage order information
- Pick & pack
- Ship to the customer
Let’s break each of these stages down.
1. Create and Manage Order Information
The basics of this process include gathering order information, validating addresses, and confirming available inventory. The next step is to combine any shipments headed for the same location before preparing them for shipment.
2. Pick & Pack
Almost every logistics company does the three-step process of picking & packing. Picking means getting ordered items off the shelves, packing is preparing them in their proper packaging, and lastly label creation.
3. Ship to the Customer
Shipping is as simple as moving the order from one place to another. If you’re a business, you’ll likely partner with a courier service such as UPS, FedEx, or USPS.
Further, here is everything you need to know about expedited shipping.
7 Common Warehouse Shipping Mistakes and Their Solutions

Follow our tips below to avoid making these seven common warehouse shipping mistakes:
- Poor inventory tracking
- Inefficient warehouse space
- Health and safety hazards
- Human errors
- Poor storage and picking system
- Inefficient order management
- Unnecessary labor costs
Let’s take a closer look at these mistakes.
1. Poor Inventory Tracking
Problem:
Your inventory is hardly organized if you often find products out of stock, lost, damaged, or broken. Perhaps you expect a product to be in a certain location, and it’s somewhere else. Or maybe you thought you had a stock of a certain product, and you don’t. These are all common signs of a messy inventory.
Basically, you’re not keeping accurate records of your inventory.
Solution:
It’s time for you to switch to a newer solution. The solution could be an inventory management system or warehouse management software. Nonetheless, technology will do you wonders!
What these systems do is gather data on your inventory. This data is sent to your software solution, which catalogs and tracks your list.
Learn more about economy shipping and why your business should offer it.
2. Inefficient Warehouse Space
Problem:
Due to rising storage costs, warehouse managers have had to find new ways to optimize their warehouse space. Unfortunately, not having enough storage is still a big issue in warehouse shipping.
Solution:
Here are a few you can use your warehousing space efficiently:
- Make use of the floor space and vertical space
- Leave enough room for employees to move around
- Automate manual processes
- Use equipment to reduce labor costs
3. Health and Safety Hazards
Problem:
You’d be surprised how often warehouse accidents take place. Heavy equipment accidents, falls and trips, exposure to chemicals, dangerous falling objects, machine entanglement, and the list goes on.
Solution:
Sadly, there is no one exact way to avoid accidents altogether. But you should always take preventive measures against them. Make sure your employees wear the right safety gear, including protective shoes. They should also wear hard hats, safety vests, and gloves.
Don’t forget to get rid of unused materials! It’ll free up space and lower potential safety hazards. Cleaning up is also key.
Moreover, avoiding these common mistakes will allow you to optimize your entire logistics operations.
4. Human Errors
Problem:
Employees are the most essential part of warehouse shipping. But some warehouses don’t have enough money to train their employees properly. Less training means more mistakes.
Solution:
Warehouses should regularly check how employees are doing and provide more training if necessary.
5. Poor Storage and Picking System
Problem:
About 50% of the labor resources are used in warehouse shipping for picking, packing, and shipping. Warehouses with bad layouts, poor equipment, and disorganized storage will experience slow picking. This is another major warehouse shipping issue.
Solution:
You need to have enough employees, and they must have a good working environment. It will help reduce human errors, shipping errors, and retrieval inefficiencies.
Also, sending orders out is just as important as receiving them. You need to have people who are dedicated to checking and receiving the goods. They will also need good material handling equipment to get the job done.
Did you know shipping and delivery aren’t the same things? Learn their differences.
6. Inefficient Order Management
Problem:
Order management is one of the most critical operations in warehouse shipping, yet it experiences the most shipping errors. The process starts the minute an order is received, then the product is shipped to the customer, and staff must handle post-purchase matters like refunds and returns. One mistake during this whole process will mess everything up, costing you time and money.
Solution:
An order management system will help manage your orders and the fulfillment process, including shipping, customer notifications, and inventory management. There are different order management systems, so choose the right one.
Check out our guide on in-house and third-party fleet management!
7. Unnecessary Labour Costs
Problem:
Today, warehouses look to invest in technology. Most warehouse managers think technology is their most expensive expense, but they often forget that manual labor doesn’t come cheap either. It’s one of the biggest warehouse expenses, costing around 50 to 70 percent of the total warehousing budget.
Solution:
First, review what needs to be done in your warehouse. Second, look at the resources you’re already using. See if you can use them more by automating more tasks. Occasionally, small businesses can share a warehouse with another company and use the leftover money to automate more tasks.
5 Warehouse Shipping Software Solutions
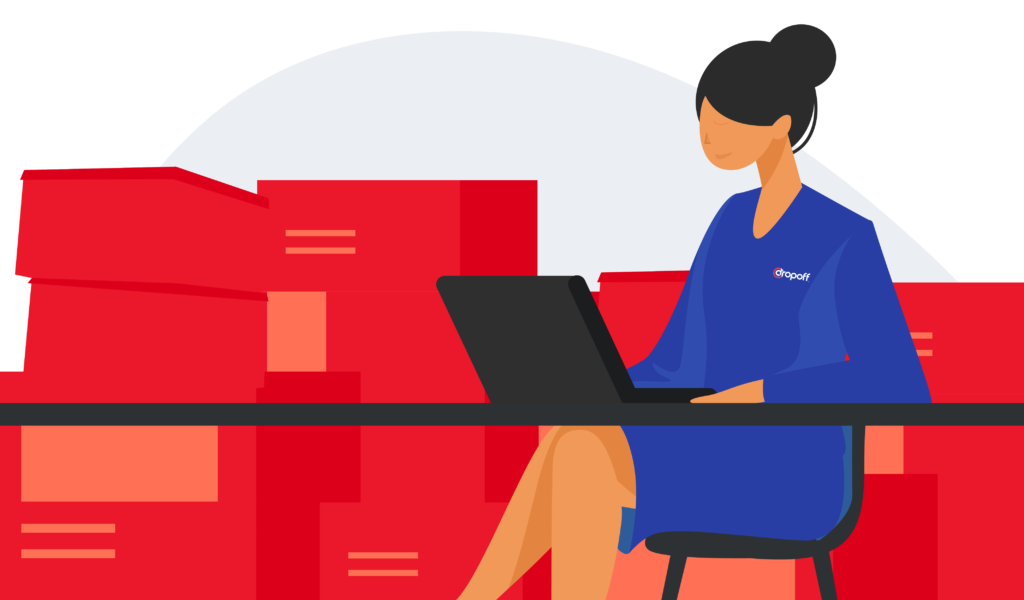
A big part of smooth shipping is using the right warehouse shipping software. We’ve listed five warehouse shipping software solutions down below.
1. NextBillion.ai
NextBillion.ai is a spatial data platform that helps companies solve complex location problems. This platform manages location data for every purpose with custom geospatial solutions.
2. Brightpearl
Brightpearl helps with things like sales and inventory. It works for retailers who have one store or multiple stores.
3. Vin eRetail
Vin eRetail is a powerful software that helps you manage your orders and inventory. It’s perfect for brands, retailers, 3PLs, marketplaces, and distributors.
4. TradeGecko
TradeGecko helps businesses manage their inventory and orders. It integrates with other software to help make it easier for companies to keep track of everything.
5. Infor
Infor provides powerful, cloud-based ERP solutions for businesses of all sizes.
How Dropoff Can Help with Warehouse Shipping
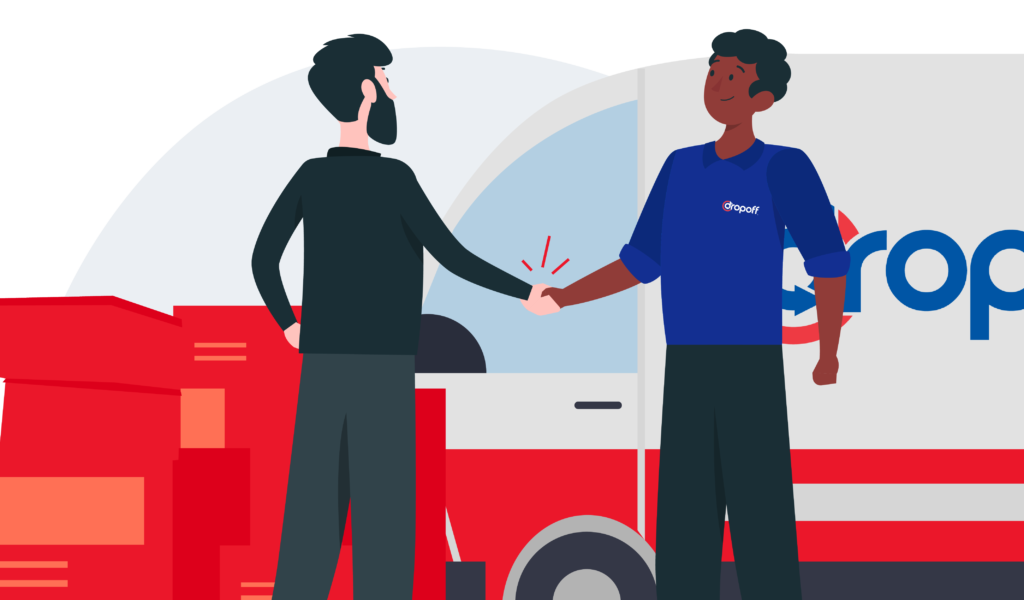
With Dropoff’s same-day delivery services, our team of expert couriers delivers items wherever they need to go. We pick items up directly from the warehouse and deliver them to the customer’s doorstep.
Our services will save you time and money. Additionally, we offer advanced real-time tracking for all deliveries.
Talk with a Dropoff expert today.
FAQs on Warehouse Shipping
1. What is warehouse shipping?
Warehouse shipping is transporting items from a warehouse to the customer’s doorstep. Furthermore, there are two types of shipping for warehouses: small parcel shipping and freight shipping.
2. How to reduce picking and packing errors?
Here are a few ways to minimize the amount of picking and packing errors:
- Find the source of the mistake.
- Organize your storage.
- Keep your technology up to date.
- Use other picking methods.
3. What is warehouse shipping and receiving?
Shipping and receiving make certain products go in and out of the warehouse correctly.
4. What does a warehouse shipping procedure look like?
Here is how the warehouse shipping procedure goes:
- Create and manage order information
- Pick, pack, and ship
- Ship to the customer