Revolutionizing Retail: The Power of Warehouse Shipping
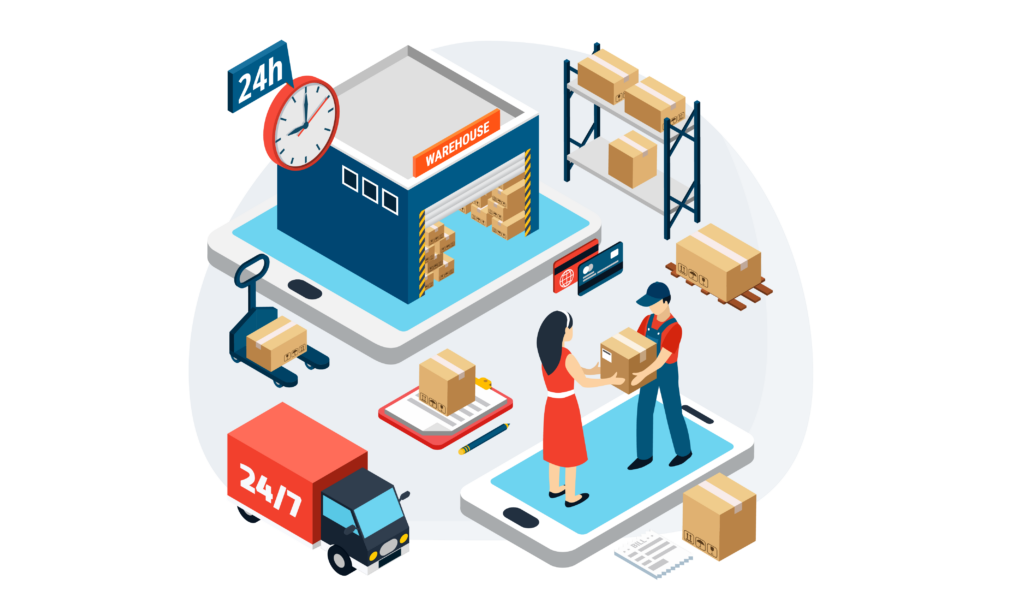
In today’s fast-paced business landscape, meeting clients’ evolving needs is paramount. Warehouse shipping, particularly the “warehouse-to-door” last-mile delivery concept, is emerging as a game-changer in building stronger customer connections.
This article explores the significance of warehouse shipping on consumers and retailers to help you decide if it’s good supply chain management that you can implement in 2024.
Understanding Warehouse Shipping
What is Warehouse Shipping?
Warehouse shipping is a well-choreographed process that is pivotal in the supply chain. It ensures that products journey from a storage facility to a customer’s doorstep efficiently and securely. At its heart lies the art of efficient inventory management, which tracks items in real-time, preventing the pitfalls of overstocking, understocking, and errors in order fulfillment.
This process extends beyond the mere movement of goods; it’s a sophisticated operation that intertwines efficiency, precision, and, most importantly, customer satisfaction. When executed seamlessly, warehouse shipping guarantees swift and safe deliveries, leaving customers with a favorable impression of your business’s unwavering commitment to their needs. Companies can cultivate robust connections with their customers and outshine competitors in the ever-evolving retail landscape by mastering these intricacies.
The Essence of Warehouse-to-Door Last-Mile Delivery
According to a recent report from Insider Intelligence, last-mile delivery accounts for 53% of the total shipping costs of a company, and 41% of all supply chain costs worldwide are actually dedicated to last-mile deliveries. This is how crucial this phase is. Failing to optimize your last-mile deliveries can truly hurt your revenue generation.
Another survey shows that 73.6% of online shoppers claim delivery is the most important aspect of the overall customer experience. Furthermore, 55% of consumers are willing to pay extra for expedited shipping, emphasizing the importance of speed and convenience in the final mile. These statistics underscore the critical role that last-mile delivery plays in shaping the perception of a brand and its connection with customers.
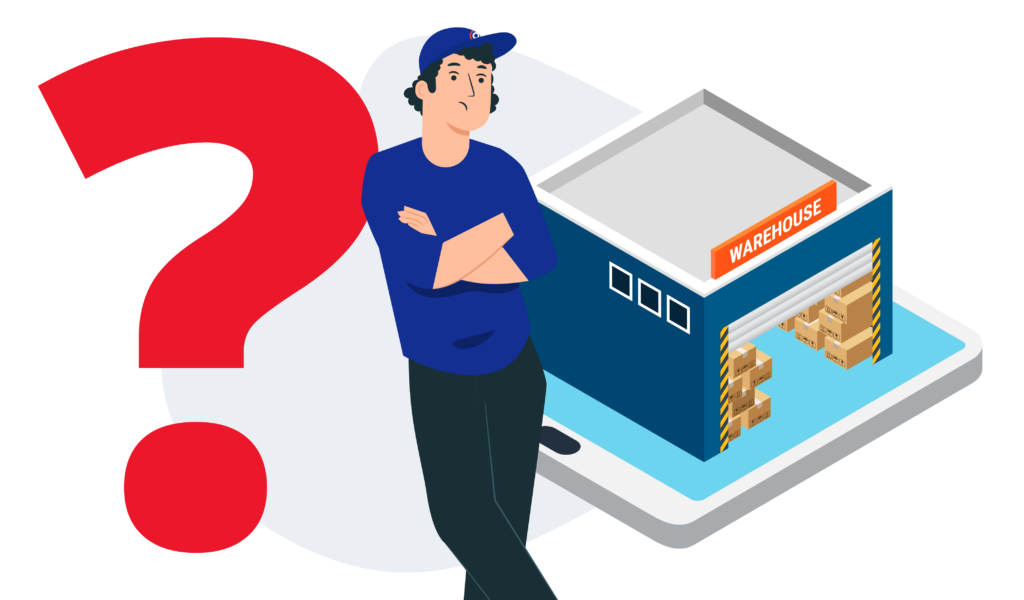
How Warehouse Delivery Works
Understanding the intricacies of how warehouse-to-warehouse shipping works is essential for both businesses and consumers. The process involves several key stages that collectively contribute to the seamless delivery of products to the customer’s doorstep:
1. Inventory Management
Inventory control is the foundation of warehouse shipment. It entails tracking and managing all products in the delivery warehouse in real-time. Accurate inventory management reduces the danger of overstocking or running out of popular items by ensuring optimal stock levels. Strong technological and software systems that deliver ongoing updates on inventory status enable this phase.
2. Order Picking
Order picking, which takes place after a customer places an order and involves either trained personnel or automated systems choosing the precise goods from the inventory required to complete the transaction, is a crucial next step. This procedure’s effectiveness guarantees that the appropriate products are selected, preventing order mistakes and guaranteeing that the consumer receives what they asked.
3. Packing
After picking the items, they move on to the “packing” stage. Here, products are carefully and securely packaged to safeguard them during transit. Packaging materials are chosen for protection and to create a positive unboxing experience for the customer, as it’s their first physical interaction with the product.
4. Labeling
During the “labeling” stage, each package is given a distinct identity. Packages have labels attached to them that frequently have barcodes, QR codes, and delivery information. These labels are essential for effective shipment tracking and tracing along their route. Customers also use these labels to identify and track incoming deliveries in real-time.
5. Coordinating Shipping Arrangements
Coordination of shipping plans is the last step in warehouse shipping. This process includes choosing the best shipment method, making transportation arrangements, and determining the best delivery routes. It takes careful coordination between different logistics partners to ensure that goods arrive at their destinations on time and with reliability.
4 Benefits of Warehouse Shipment for Consumers
While relatively new, a significant number of consumers now experience the benefits of warehouse shipping.
1. Speed
By streamlining the supply chain, products reach consumers with remarkable swiftness. Same-day and next-day delivery options have become commonplace, allowing customers to get their hands on desired items faster. On-time delivery and warehouse management enhance overall convenience, particularly for time-sensitive purchases.
2. Convenience
This warehouse-to-door delivery eliminates the need for consumers to travel to physical stores, sparing them the hassles of traffic, long queues, and store hours. It also allows for round-the-clock shopping, accommodating modern consumers’ diverse schedules and preferences.
3. Real-Time Tracking
Warehouse shipping integrates advanced tracking technology that allows consumers to monitor their orders at every journey stage. This transparency instills confidence and empowers customers with precise delivery information, eliminating the guesswork about when their packages will arrive.
4. Enhanced Customer Experience
Perhaps the most significant benefit of warehouse shipping is enhancing the overall customer experience. When products are delivered promptly, intact, and as expected, customers become satisfied and loyal. Positive experiences lead to repeat business and advocacy, strengthening consumer and business bonds.
5 Benefits of Warehouse Shipping for Retailers and Businesses
Consequently, the rise of warehouse shipping has also brought numerous advantages to business owners. Here are some of them:
1. Speed of Delivery
Speedy deliveries set your business apart from competitors, attracting customers who prioritize timely receipt of their orders. This enhanced efficiency results in higher customer satisfaction and can lead to increased customer loyalty.
2. Reduced Costs
Streamlined processes and improved courier management result in reduced storage costs, fewer errors, and a more efficient workforce. Last-mile delivery operations are also optimized, translating to lower fuel consumption and reduced transportation expenses.
3. Unique Value Proposition
Offering customers various delivery options, including same-day and flexible delivery slots, can be a unique selling point. Moreover, businesses can provide exceptional tracking and real-time communication features, further enhancing the customer experience and driving sales.
4. Sustainability
Warehouse shipping allows companies to reduce their environmental footprint. Efficient last-mile delivery operations, including logistics optimization and eco-friendly delivery vehicles, contribute to a smaller carbon footprint.
5. Data-Driven Insights
Businesses can harness this information to gain valuable insights into consumer behavior, demand patterns, and operational efficiency.
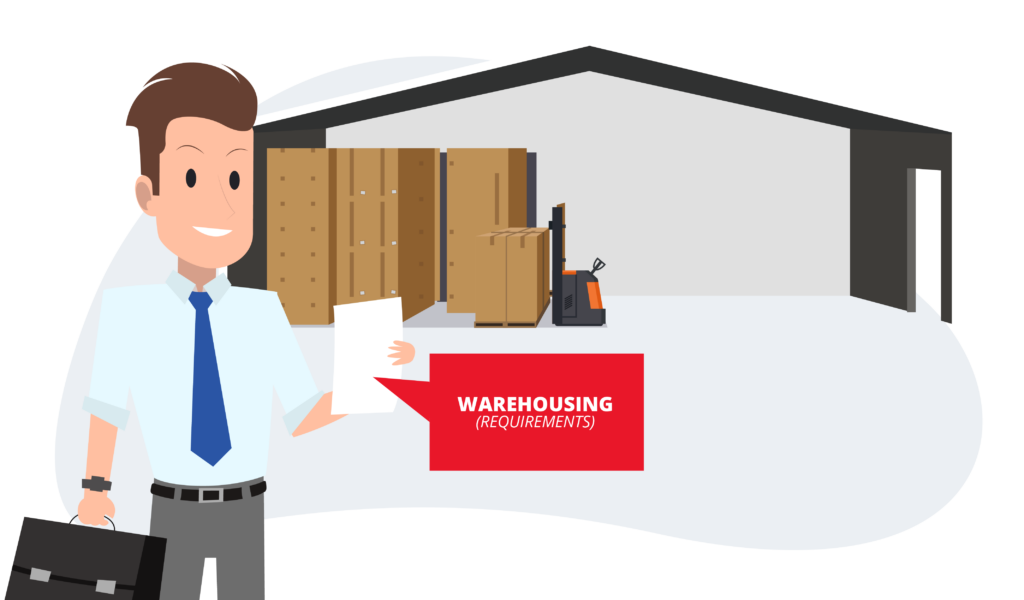
7 Warehouse Requirements for Efficient Shipping
While warehouse shipping is a lucrative supply chain method, it requires highly efficient warehouse management.
1. Inventory Management
A robust inventory management system ensures that each product’s quantity, location, and status are constantly monitored. This real-time tracking prevents overstocking, understocking, and costly errors in order fulfillment.
2. Optimized Layout
An optimized layout ensures that products are stored in a manner that minimizes the time and effort required for retrieval. Items with higher demand should be easily accessible, and storage should be organized logically.
3. Order Accuracy
Implementing quality control measures, barcode scanning, and double-check processes can help maintain high order accuracy. Ensuring that the right products are picked and packed for each order is essential.
4. Peak Season Demands
Scaling warehouse operations to meet these peak season demands is crucial. This may involve hiring temporary staff, optimizing work schedules, and expanding storage capacity.
5. Technology Integration
Warehouse management systems (WMS) and automated picking systems can streamline operations, reduce human error, and provide real-time data for informed decision-making.
6. Safety and Security
Employee safety should be a top priority, with proper training, equipment, and safety protocols in place. Security measures should also protect the warehouse from theft, damage, or unauthorized access.
7. Sustainability
Efficient lighting, insulation, and eco-friendly packaging can reduce energy consumption for heightened cost-saving and lower environmental impact.
7 Technology and Innovations in Warehouse Shipping
Businesses are increasingly harnessing cutting-edge technology and logistics innovations to remain competitive and meet the evolving demands of consumers. Key areas of innovation include:
1. Warehouse Management Systems (WMS)
WMS provides real-time insights into inventory, order processing, and shipment tracking. These systems offer features like intelligent order routing, inventory visibility, and performance analytics, enabling businesses to manage their warehouses with unparalleled efficiency.
2. Automation and Robotics
Automation has made significant strides in the warehouse industry. Robotics, including autonomous mobile robots (AMRs) and automated guided vehicles (AGVs), can swiftly navigate the warehouse, locate products, and transport them to the packing station, reducing the need for manual labor and minimizing the risk of human error.
3. Artificial Intelligence (AI) and Machine Learning
Machine learning algorithms can predict demand patterns, helping businesses allocate stock efficiently. AI-powered chatbots and virtual assistants enhance customer support and order tracking.
4. Internet of Things (IoT)
Sensors and RFID technology can track the movement of products, monitor environmental conditions, and provide real-time alerts in case of logistical issues like temperature deviations or unauthorized access.
5. Cloud Computing
Cloud solutions enable seamless integration with e-commerce platforms, facilitating order placement and tracking, and they are especially valuable for businesses with multiple warehouses.
6. Drones and Autonomous Vehicles
Drones and autonomous delivery vehicles are being experimented with for last-mile delivery. These innovative modes of transportation can navigate urban landscapes and reach customers quickly, especially in congested areas.
7. Blockchain Technology
Blockchain provides an immutable ledger that tracks the history of products, from the manufacturer to the customer, ensuring the authenticity and quality of products.
Best Practices in Warehouse Shipping
Thinking of going all-in for warehouse shipping? Here are some of the best practices you can emulate:
Process Standardization
Well-defined processes help reduce errors, minimize inefficiencies, and enhance productivity. This involves creating clear and documented workflows for order picking, packing, labeling, and quality control tasks.
Training and Skill Development
Invest in ongoing training to ensure employees are proficient in their tasks and updated on the latest technologies. A skilled workforce is more adaptable and capable of handling peak seasons and unexpected challenges.
Inventory Accuracy
Real-time inventory accuracy is non-negotiable. Use advanced warehouse management systems (WMS) and barcoding technology to monitor inventory levels. Regular cycle counts and reconciliations help keep inventory discrepancies to a minimum.
Efficient Picking and Packing
Use automation or robotic systems to assist with picking, reducing human error. Similarly, efficient packing stations equipped with necessary supplies and clear instructions expedite order preparation.
Clear Labeling and Packaging
Ensure each package is accurately labeled with the necessary tracking information, shipping labels, and customer-specific details. A well-labeled package minimizes the chances of misdelivery.
Data Analytics
Leverage data analytics to gain insights into inventory trends, order volume, and customer preferences. This information can guide inventory management, stocking decisions, and marketing strategies, ultimately enhancing customer satisfaction and sales.
Customer Communication
Notify customers of order updates, delivery tracking, and any potential delays. Excellent customer service can mitigate issues and lead to greater customer satisfaction.
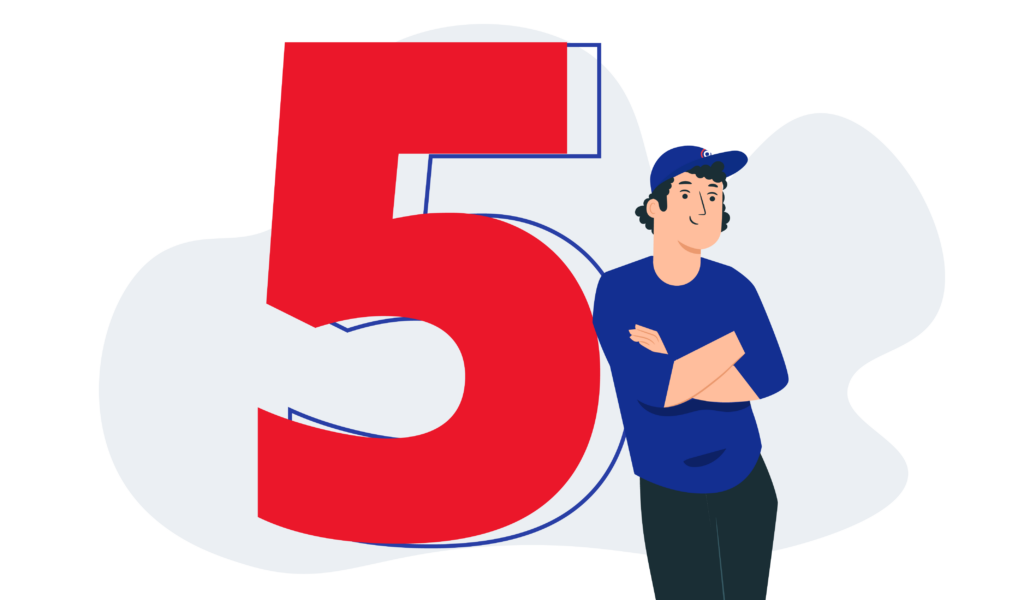
5 Signs that Your Company Should Start Working with Warehouse Shipping Delivery
To determine if this is the right move for your company, consider the following five signs that suggest your business is well-positioned to benefit from warehouse shipping:
Rising Customer Expectations
If your customers increasingly demand faster deliveries, flexible delivery options, and real-time order tracking, it’s a clear sign that you should explore warehouse shipping.
Inventory Management Challenges
Are you struggling with inventory management issues, such as overstocking, understocking, or poor order accuracy? Warehouse shipping involves precise inventory tracking, reducing these problems and ensuring you always have the right products in stock.
Scalability Concerns
If your business experiences seasonal peak demand or anticipates rapid growth, warehouse shipping can provide the scalability required to handle increased order volumes efficiently.
Competitive Landscape
If your competitors are already offering warehouse shipping or expedited delivery options, not doing so may put your business at a disadvantage. Customers often choose businesses that can provide faster and more convenient delivery options, making warehouse shipping a competitive necessity in certain markets.
Operational Efficiency Goals
The streamlined processes and reduced error rates associated with warehouse shipping can lead to cost savings and enhance overall operational efficiency.

How Dropoff Can Help Businesses Start Working with Warehouse Shipping
Dropoff, a same-day delivery courier, offers businesses efficient warehouse and delivery services. By emphasizing support, advanced technology, and unparalleled expertise, Dropoff empowers businesses to excel in warehouse shipping.
Dropoff becomes an extension of your brand, guaranteeing a professional and reliable experience with each phase of warehousing and shipping. Our drivers are thoroughly vetted, experienced, and professional, ensuring your items are handled carefully and well. Focusing on customized logistics, Dropoff adapts to your business needs and provides 24/7 local customer service support. This adaptability, coupled with their data-backed on-time guarantee, instills confidence in the reliability of their service.
FAQ
Warehouse shipping is efficiently managing inventory, picking, packing, labeling, and shipping products from a storage facility to the final destination, typically a customer’s doorstep.
The objectives of warehouse shipping are to streamline the supply chain, meet customer expectations for fast and convenient delivery, reduce costs, and enhance the overall customer experience.
Warehouse last-mile delivery is handled by meticulously coordinating order picking, packing, labeling, and selecting efficient shipping arrangements to ensure products are delivered promptly and accurately to the customer’s doorstep.